What is the gas obtained by roasting of sulphide ore?
Let’s break down why sulfur dioxide formation is so important in this process.
First, the sulfur dioxide produced during roasting is actually a valuable resource. It’s often used to produce sulfuric acid, which is a vital chemical used in various industries.
Second, the formation of sulfur dioxide helps to remove sulfur from the ore, which is essential for producing pure metals. You see, sulfide ores often contain a significant amount of sulfur, and this sulfur needs to be removed to obtain a high-purity metal. By converting the sulfur to sulfur dioxide gas, you can easily remove it from the ore.
Third, the process of roasting helps to convert the sulfide ore into a more reactive form, which makes it easier to extract the metal. For example, when you roast copper sulfide, you convert it to copper oxide, which is much more easily reduced to copper metal than the sulfide form.
So, to summarize, sulfur dioxide is the gas produced when you roast sulfide ores, and it plays a vital role in metal extraction by providing a valuable resource, removing sulfur from the ore, and making the ore more reactive for metal extraction.
What happens when sulphide ore is roasted?
Let’s break this down a bit further:
Sulphide ores: These are naturally occurring minerals where the metal is chemically combined with sulfur. Examples include galena (lead sulfide, PbS), cinnabar (mercury sulfide, HgS), and sphalerite (zinc sulfide, ZnS).
Oxides: During roasting, the sulfur in the sulphide ore reacts with oxygen from the air, forming sulfur dioxide gas (SO2). This leaves behind the metal oxide. For example, when we roast galena (PbS), it converts to lead oxide (PbO):
2PbS + 3O2 → 2PbO + 2SO2
Purification: Roasting plays a critical role in purifying metals because the volatile impurities and moisture are removed during the process. This results in a more concentrated and purer form of the metal oxide, making it easier to extract the metal itself.
In addition to the purification aspect, roasting serves another vital purpose:
Preparation for further processing: The metal oxides produced during roasting are often used as feedstock for further processing steps such as smelting. Smelting involves the reduction of the metal oxide using a reducing agent like carbon to extract the pure metal.
Roasting is a fundamental process in extractive metallurgy, and understanding its importance helps us appreciate how we obtain metals from their ores.
What is the product of the roasting of sulphide ore?
Let’s break down why:
Imagine you have a sulfide ore like galena (lead sulfide, PbS). When you roast it, you’re essentially reacting it with oxygen in a controlled way. The heat of the roasting process causes the sulfide to react with oxygen, forming lead oxide (PbO) and releasing sulfur dioxide gas (SO2). This reaction can be represented by the following chemical equation:
2PbS + 3O2 → 2PbO + 2SO2
The lead oxide produced through roasting is then further processed to extract the metallic lead. This typically involves a process called smelting, where the lead oxide is heated with a reducing agent, like carbon, to convert it back into metallic lead.
Roasting is a crucial step in the extraction of many metals from sulfide ores. It’s a way to convert the sulfide into a more manageable form (oxide) that can be further processed to extract the desired metal.
This process is not about direct conversion to the metallic form, but rather a necessary step towards that goal. Think of it as a bridge between the raw ore and the final metal product. Roasting prepares the ore for the next stage in the extraction process, where the metal can be finally isolated.
Is sulphide ore roasting or calcination?
The simple answer is that metal oxides are generally more stable than metal sulfides. This means it’s easier to extract the metal from its oxide form compared to its sulfide form.
Roasting is a process that converts the sulfide ore into an oxide by reacting it with oxygen in the air. This process involves heating the ore to a high temperature, allowing the sulfur to react with oxygen and form sulfur dioxide gas.
Here’s a more detailed explanation:
Imagine you have a sulfide ore like pyrite (FeS2). Pyrite is a sulfide ore of iron. To get the iron out, we need to remove the sulfur. Roasting the pyrite with air allows us to achieve this:
2FeS2 + 11/2 O2 → Fe2O3 + 4SO2
This reaction converts the iron sulfide (FeS2) into iron oxide (Fe2O3), releasing sulfur dioxide gas (SO2). The iron oxide can then be more easily reduced to iron using a reducing agent like carbon.
Roasting is a key step in the metallurgical process of extracting metals from their ores. It’s a thermochemical process that makes it much easier to get the metal out.
So, in summary, we roast sulfide ores to convert them into oxides because:
1. Metal oxides are generally more stable than metal sulfides.
2. Roasting allows for the removal of sulfur as sulfur dioxide gas.
3. The resulting metal oxide is easier to reduce to the metal.
This process is essential for efficiently extracting many important metals from their sulfide ores.
What gas is released during roasting?
Sulfur dioxide is a colorless gas with a pungent odor. It is a common air pollutant and can be harmful to human health. However, in the context of roasting, the release of sulfur dioxide is actually a beneficial outcome. This gas can be captured and used in the production of sulfuric acid, a valuable industrial chemical.
The conversion of metal sulfide to metal oxide is a complex chemical reaction that involves several steps. The first step is the oxidation of the sulfide to sulfur dioxide. This reaction is exothermic, meaning that it releases heat. The heat from this reaction can be used to drive the subsequent steps of the roasting process.
The second step in the roasting process is the reduction of the metal oxide to the metal. This reaction is endothermic, meaning that it requires heat. The heat for this reaction can be supplied by the exothermic oxidation reaction.
The roasting process is an important step in the production of many metals, including copper, zinc, and lead. It is a relatively simple and efficient process, and it is an important part of the global economy.
What is the roasting method of sulphide ore?
Let’s break down how roasting works and why it’s so important for sulfide ores:
The Chemistry Behind Roasting:
1. Oxidation: The heat applied during roasting allows oxygen from the air to react with the sulfide minerals in the ore. This reaction converts the sulfides (like copper sulfide or lead sulfide) into their respective oxides (copper oxide or lead oxide).
2. Removal of Sulfur: A significant part of the sulfur present in the ore is released as sulfur dioxide gas during the roasting process. This sulfur dioxide gas can be collected and further processed to produce sulfuric acid, a valuable industrial product.
Why Roasting is Crucial for Sulfide Ores:
1. Increased Reactivity: By converting sulfides into oxides, roasting makes the ore more reactive. This increased reactivity allows for easier extraction of the desired metal through subsequent processes like smelting.
2. Easier Smelting: Smelting, the process of melting and separating the metal from the ore, is much more efficient when the ore is in its oxide form. Roasting ensures the ore is in the right form for smelting to take place.
3. Byproduct Recovery: The sulfur dioxide released during roasting is not just a waste product. It can be captured and used to produce sulfuric acid, which is a valuable commodity in various industries.
In summary, roasting is a vital step in the extraction of metals from sulfide ores. It’s a high-temperature process that changes the chemical composition of the ore, making it easier to extract the desired metal and generating valuable byproducts like sulfuric acid.
What happens when sulphur is roasted?
Think of it like this: Imagine a campfire. When you burn wood, the oxygen in the air reacts with the carbon in the wood, producing carbon dioxide and ash. The ash represents the metal oxides formed during roasting. Roasting essentially converts the sulfur and the metal in the ore into more manageable forms, setting the stage for further processing to extract the desired metal.
The precise reactions that occur during roasting depend on the specific metal and sulfide ore being processed. For example, when roasting copper sulfide (CuS), the primary reactions are:
* CuS + O2 –> CuO + SO2
* 2CuS + 3O2 –> 2CuO + 2SO2
These reactions produce copper oxide (CuO) and sulfur dioxide (SO2). The copper oxide can then be further processed to obtain pure copper.
In summary, roasting is a chemical process that utilizes oxygen to transform sulfur in sulfide ores into sulfur dioxide gas and the metal into metal oxides and metal sulfates. This transformation lays the foundation for extracting the desired metal from the ore in subsequent processing steps.
See more here: What Happens When Sulphide Ore Is Roasted? | The Gas Evolved During Roasting Of Sulphide Ore Is
What is the process of roasting sulfide?
Oxidation is the key player here. It’s the process of adding oxygen to the sulfide minerals. Imagine it like adding air to a fire; it helps the reaction burn hotter and faster. Reduction is the opposite; it involves removing oxygen. Chlorination, sulfation, and pyrohydrolysis are other chemical reactions that can occur during roasting, depending on the specific minerals being roasted and the roasting conditions.
Think of it like this: Roasting is a bit like cooking. You start with raw ingredients (sulfide minerals), add heat, and through a series of chemical changes, you get a new, transformed product. The specific products you get depend on what you start with and how you cook it.
Let’s dive a bit deeper into oxidation. Imagine you have a sulfide mineral like pyrite, also known as “fool’s gold.” Pyrite is made up of iron and sulfur (FeS2). When you roast pyrite, the sulfur reacts with oxygen from the hot air, creating sulfur dioxide gas (SO2). This gas is actually a valuable byproduct that can be used to make sulfuric acid! The iron in the pyrite is also transformed, typically forming iron oxide (FeO).
Roasting is a powerful tool used in mining and metallurgy. It’s a crucial step in extracting valuable metals like copper, lead, zinc, and nickel from their ores.
What is roasting a sulfide ore?
Roasting is a critical step in processing some ores. It helps remove impurities and prepare the ore for further processing. Roasting is a gas-solid reaction that occurs at high temperatures. The heat helps to break down the sulfide ore and release the metal. The process is used to extract metals like copper, lead, zinc, and nickel from their ores.
During roasting, the sulfide ore reacts with oxygen in the air to form oxides, sulfates, or other compounds. The reactions that take place during roasting depend on the type of ore and the temperature used.
Here’s how roasting works:
Oxidation: The heat causes the sulfide minerals in the ore to react with oxygen, forming metal oxides and sulfur dioxide gas.
Calcination: If the temperature is high enough, the metal oxides can be further converted to their metallic forms.
Sintering: The roasted ore is often sintered to improve its physical properties. Sintering is a process that involves heating the ore to a temperature where the particles partially melt and bond together. This makes the ore easier to handle and process.
Roasting can be performed in several ways, depending on the specific ore and the desired product. Some common roasting methods include:
Heap roasting: This method is used for low-grade ores. The ore is piled in a large heap and ignited. Air is drawn through the heap, which helps to oxidize the sulfide minerals.
Kiln roasting: This method is used for higher-grade ores. The ore is heated in a rotating kiln, which allows for more efficient heat transfer.
Fluidized bed roasting: This method involves suspending the ore particles in a stream of air. The air helps to heat the ore and also provides the oxygen necessary for oxidation.
Roasting is a complex process that requires careful control of temperature, air flow, and other factors to ensure that the desired products are formed. The process is used in many different industries to produce a wide variety of metals and other products.
What determines the composition of a product in sulfide roasting?
The composition of a product in sulfide roasting is a delicate balance of various factors. It’s not just about the chemical and mineralogical composition of the concentrate, temperature, and partial pressures of O2, SO2, and SO3. Other crucial process parameters play a significant role. Think of it like a recipe, where you need the right ingredients and the perfect cooking time for a delicious outcome.
Particle size, mixing, reaction time, and the roasting technique all contribute to the final product. Imagine you’re roasting a whole chicken versus roasting chicken pieces. They require different temperatures, times, and approaches, right? It’s the same principle with sulfide roasting.
Particle size is important because it affects how quickly oxygen can reach the sulfide minerals. Think of it like a pile of sand. The smaller the sand particles, the more surface area is exposed to the air.
Mixing is vital to ensure the even distribution of heat and oxygen throughout the concentrate. It helps ensure all the sulfide minerals are exposed to the right conditions. Just like when you stir your batter to ensure it’s evenly mixed!
Reaction time is another important factor. It determines how much time the sulfides have to react with the oxygen, and ultimately how much sulfur is removed. Imagine you’re baking a cake. You can’t just toss it in the oven and expect it to be done in five minutes. It needs a specific amount of time to bake through.
Finally, the roasting technique itself plays a role. Different techniques involve different temperatures, oxygen levels, and airflow patterns. Some techniques are designed for specific types of concentrates, while others are more versatile.
Think of sulfide roasting as a carefully orchestrated dance between these factors. Getting the right combination can be tricky, but it’s essential to achieve the desired product composition, which is crucial for downstream processes like smelting.
Why is sulfide roasting an autogenous process?
Let me explain. The heat generated from the roasting reaction is sufficient to maintain the roasting temperature. So, you don’t need to add extra fuel to keep the process going. Think of it like a self-sustaining fire. The heat from the burning wood keeps the fire going, and the fire keeps producing heat.
This is why sulfide roasting is considered autogenous. The process is driven by the heat released during the reaction, without the need for external fuel sources.
Now, let’s delve a little deeper into why this process is so efficient. The heat generated during the roasting process comes from the chemical reaction between the sulfide minerals and oxygen. This reaction produces sulfur dioxide gas, which is released into the atmosphere. The energy released during this reaction is enough to maintain the temperature needed for the roasting process.
Imagine the reaction like a chain reaction: the heat from the initial reaction triggers more reactions, releasing even more heat, and so on. This self-sustaining nature of sulfide roasting makes it an efficient and cost-effective way to process sulfide ores.
The amount of heat produced during the roasting process depends on several factors, including the type of sulfide ore being roasted, the temperature at which the roasting is carried out, and the amount of oxygen available.
For example, roasting sulfide ores containing iron, such as pyrite (FeS2), produces a significant amount of heat due to the formation of iron oxide (Fe2O3). This heat can be used to preheat the incoming ore, further enhancing the efficiency of the roasting process.
Overall, sulfide roasting is a fascinating example of how chemical reactions can be used to create self-sustaining processes. The heat generated by the reaction is enough to drive the process, making it an efficient and cost-effective way to extract metals from sulfide ores.
See more new information: barkmanoil.com
The Gas Evolved During Roasting Of Sulphide Ore Is | What Is The Gas Obtained By Roasting Of Sulphide Ore?
Now, the key gas evolved during roasting of sulfide ores is sulfur dioxide, also known as SO2. It’s a colorless gas with a pungent odor, and it’s the result of the chemical reaction between the sulfide in the ore and oxygen from the air.
But why is this gas so important? Well, it plays a crucial role in the extraction process. Let’s break it down.
The Chemistry Behind Roasting
Imagine you have a sulfide ore, like copper sulfide (CuS). When you heat this ore in the presence of air, the sulfur in the sulfide combines with oxygen to form sulfur dioxide. The chemical equation for this reaction is:
2CuS + 3O2 → 2CuO + 2SO2
This reaction is exothermic, meaning it releases heat. And that’s a good thing because it helps maintain the high temperature needed for roasting.
The sulfur dioxide gas is then collected and used in various applications. One of the most common uses is the production of sulfuric acid, a highly important industrial chemical.
Benefits of Roasting
Roasting offers several advantages in metal extraction:
Conversion of Sulfide to Oxide: Roasting converts the sulfide ore into an oxide, which is a more suitable form for further processing. For example, copper sulfide is converted into copper oxide (CuO), which is more readily reduced to copper metal.
Removal of Impurities: Roasting can also help remove impurities from the ore. For instance, arsenic and antimony are often present in sulfide ores, and roasting can volatilize these impurities, removing them from the ore.
Preparation for Smelting: The oxide formed during roasting is easier to smelt, a process where the oxide is reduced to the metal using a reducing agent like carbon.
Types of Roasting
Roasting can be classified into different types based on the desired outcome:
Oxidizing Roasting: This type of roasting aims to convert sulfides into oxides. It’s the most common type of roasting and is used for extracting metals like copper, lead, and zinc.
Chlorinating Roasting: This process involves reacting the sulfide ore with chlorine gas, converting the sulfide into a chloride. Chlorinating roasting is particularly useful for extracting metals like gold and silver.
Reducing Roasting: This type of roasting involves reacting the sulfide ore with a reducing agent, like carbon, to directly produce the metal. This process is typically used for extracting metals like mercury and arsenic.
Environmental Considerations
While roasting is an essential process in metal extraction, it’s also important to consider its environmental impact. The sulfur dioxide gas released during roasting is a major air pollutant, contributing to acid rain and respiratory problems.
Therefore, modern roasting processes often incorporate pollution control technologies to capture and treat the sulfur dioxide before it is released into the atmosphere.
FAQs
Q: What is the gas evolved during the roasting of sulfide ore?
A: The main gas evolved during the roasting of sulfide ore is sulfur dioxide (SO2).
Q: What happens to the sulfur dioxide gas released during roasting?
A: The sulfur dioxide gas is often collected and used to produce sulfuric acid (H2SO4), a vital industrial chemical.
Q: What are the benefits of roasting sulfide ores?
A: Roasting converts sulfides to oxides, removes impurities, and prepares the ore for smelting, making metal extraction more efficient.
Q: What are the environmental concerns associated with roasting?
A: Sulfur dioxide (SO2) gas released during roasting is a major air pollutant, contributing to acid rain and respiratory issues. Modern roasting processes include pollution control technologies to minimize these impacts.
Q: What are the different types of roasting?
A: Roasting can be categorized into oxidizing, chlorinating, and reducing roasting, each tailored for different metal extraction processes.
Roasting, with its complex chemistry and environmental implications, is a fascinating aspect of metallurgy. It showcases the importance of understanding chemical reactions and managing environmental impacts in the quest for valuable metals.
Lecture 15: Thermodynamics of roasting Contents – 911 Metallurgist
Whether roast product is oxide or sulphate or partially sulphide would depend on temperature and partial pressures. The purpose of this lecture is to determine 911 Metallurgist
ROASTING OF SULFIDE MINERALS – Wiley Online Library
gas is passed upward through a bed of solid particles of small and preferably regular size in the range 2–0.02mm diameter, the behavior of the bed will depend upon the velocity of Wiley Online Library
Roasting of sulphide ore gives the gas (A).(A) is a colourless gas …
Which of the following statements, about the advantage of roasting of sulphide ore before reduction is not true? Match items in Column – I with the items of Column – II and assign Shaalaa.com
Roasting of Sulfide Minerals – ResearchGate
The roasting of sulfide ores and concentrates is one of the most important steps in pyrometallurgical metal production from primary raw materials, due to the ResearchGate
Roasting of Sulfide Minerals – Wiley Online Library
In the extraction of metals from sulfides, roasting is applied to achieve different objectives depending on the overall process flow sheet. Such objectives include Wiley Online Library
Roasting (metallurgy) – Wikipedia
During roasting, the sulfide is converted to an oxide, and sulfur is released as sulfur dioxide, a gas. For the ores Cu 2 S ( chalcocite) and ZnS ( sphalerite ), balanced equations for the roasting are: 2 Cu 2 S + 3 O 2 Wikipedia
Sulfide Ore – an overview | ScienceDirect Topics
Sulphide ores are a major source of Cu, Ni and precious metals. A basic principle of the extraction processes is to blow air into the molten sulphide in order to oxidise (1) S, ScienceDirect
PYRITE ROASTING, AN ALTERNATIVE TO SULPHUR BURNING
The roasting of sulphide ores and concentrates is often the first step in the production of metals or chemicals. In many processes, the production of sulphuric acid is viewed as a saimm.co.za
To Show That Hydrogen Gas Is Evolved By The Action Of Acid On Metals
Roasting Of Sulphides
Roasting Of Sulphides Given The Gas X As A By Producet. This Is A Colortess Gas With Choking Sme…
Froth Flotation Process@Sulphide Ore
Roasting Ore
Roasting Gold Ore – Small Scale Hard Rock Mining – Colorado Gold – Denver Gold.
Link to this article: the gas evolved during roasting of sulphide ore is.
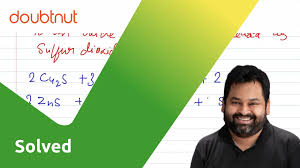
See more articles in the same category here: https://barkmanoil.com/bio/